Hey guys I swapped my 3.33" S Trim pulley for a 3.13" last night in hopes of hitting the magical 15#'s of boost. To my suprise I fell from a previous high of 12.8 back to 11.8-12.0. I think I have good belt wrap and it's already so tight I could play it like a guitar. I see no belt dust either. I'm beginning to wonder if it's belt slip or if I have a leaking hose. If I had a leak my AFR's would log really rich though right? My boost curve is really linear, just lower than before. Is there some sort of belt dressing I can apply just to verify if it's indeed belt slip? If it is I just can't see getting the belt any tighter.
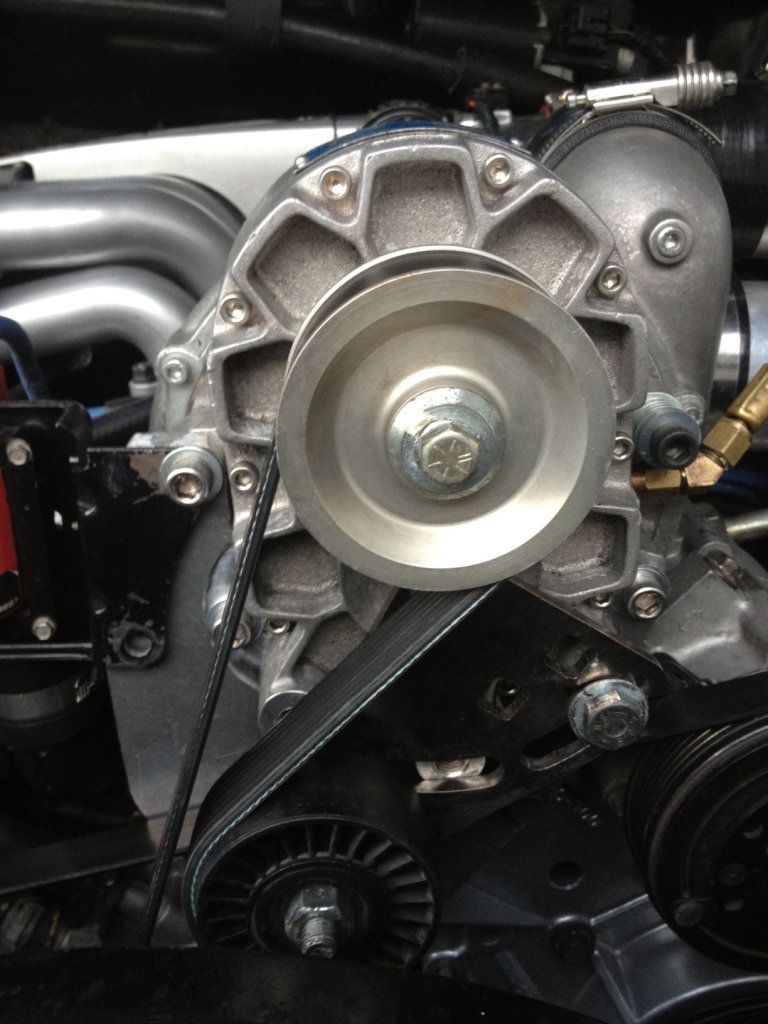
If I can verify the issue to be belt slip then I'll have a custom lower made so I can swap out the outer ring from a Gen 2 Lightning. 10" lower and 3.33" upper should put me just above 50,000 rpm by 5000 rpm on the tach. I would like to keep a 5000 RPM shift point.
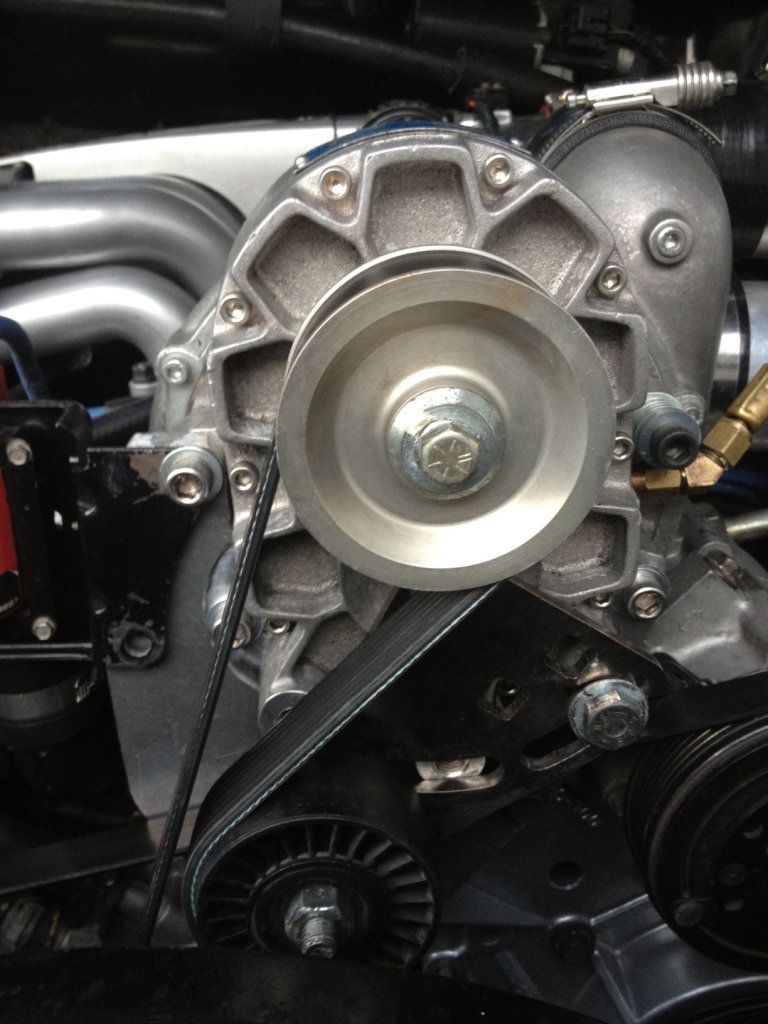
If I can verify the issue to be belt slip then I'll have a custom lower made so I can swap out the outer ring from a Gen 2 Lightning. 10" lower and 3.33" upper should put me just above 50,000 rpm by 5000 rpm on the tach. I would like to keep a 5000 RPM shift point.
Comment