Has anyone ever heard of this, or see it happen? I was reading this thread on another board, I think it's some kind of urban legend.
A google search pulls up some discussions, but no hard evidence.
I mean the paint is cured at 350-450*, not like that is going to change the properties of a wheel, they prolly get close to that temp on a road course.
Thoughts?
A google search pulls up some discussions, but no hard evidence.
I mean the paint is cured at 350-450*, not like that is going to change the properties of a wheel, they prolly get close to that temp on a road course.
Thoughts?
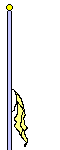
Comment